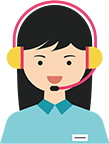
Key Facts about Concrete Materials Based on Ready-Mix Concrete Plants (Part 2)
Introduction
In this article, we will continue our exploration of concrete materials based on ready-mix concrete plants. Understanding the properties and characteristics of various components is essential for optimizing concrete construction projects. In this second part, we will delve into important aspects such as the preference for medium sand in pumpable concrete, particle grading of aggregates, quality requirements for aggregates, the use of fly ash in pumpable concrete, and the different types of concrete admixtures. Let's dive in!
11. The Preference for Medium Sand in Pumpable Concrete
When it comes to pumpable concrete, medium sand is often the preferred choice. This is due to the rational grading of medium sand, with a particle content below 0.3mm reaching around 15%. These particles in the mortar of the concrete adhere closely to the inner wall of the pumping pipe, resulting in minimal friction resistance and facilitating the pumping process. Coarse sand, on the other hand, has higher friction resistance, which hinders pumping. Additionally, fine sand has a larger surface area, requiring more cement to achieve the same strength, thereby increasing the risk of cracking.
12. Particle Grading of Aggregates
Aggregates can be classified into two types based on particle grading: single particle grading and continuous particle grading. The single particle grading includes 10-20, 16-31.5, and 20-40, while the continuous particle grading includes 5-10, 5-16, 5-25, 5-31.5, and 5-40.
13. Preference for Continuous Particle Grading in Pumpable Concrete
In pumpable concrete, it is preferable to use aggregates with continuous particle grading. Compared to single particle grading with the same maximum particle size, continuous particle grading has a lower void ratio, meaning fewer voids that need to be filled with mortar. For the same volume of concrete under the same conditions, the surface area of the aggregates using single particle grading is larger, requiring a higher cement content. Moreover, pumpable concrete made with continuous particle grading exhibits better workability, making it more suitable for pumping construction. Therefore, continuous particle grading should be prioritized in pumpable concrete.
14. Key Quality Requirements for Aggregates
Good-quality aggregates must meet several requirements, including:
- The particle size should comply with the specifications, with continuous particle grading.
- They should be free from yellow skin (surface mud), large lumps of clay, and oversized particles.
- The content of needle-shaped and flaky particles should be minimized, with the needle-like and flaky particle content not exceeding 10% for aggregates used in pumpable concrete.
- The shale content should be minimized since shale has lower strength and increases the content of flaky particles.
15. Quality Requirements for Sand
High-quality sand should meet the following requirements:
- The particle grading should be within the specified range.
- It should be free from impurities such as clay, organic matter, and harmful chemicals.
- The sand should have a low mud content.
16. Importance of High-Quality Aggregates
Using high-quality aggregates in concrete construction is crucial for several reasons:
- High-quality aggregates contribute to the strength and durability of concrete.
- They help reduce the risk of cracking and enhance the workability of the concrete mixture.
- Good-quality aggregates ensure the stability and long-term performance of the concrete structure.
- They improve the pumping efficiency of concrete, making construction processes more efficient.
17. Cementitious Material Classification
Cementitious materials can be classified into several grades:
- Class I: Ordinary Portland cement (OPC) with strength grades of 32.5, 42.5, and 52.5.
- Class II: Moderate heat Portland cement with strength grades of 32.5, 42.5, and 52.5.
- Class III: Low heat Portland cement with strength grades of 32.5, 42.5, and 52.5.
- Class IV: Sulfate-resistant cement.
- Class V: Composite Portland cement with a strength grade of C15 to C40.
18. The Addition of Fly Ash in Pumpable Concrete
Fly ash is added to pumpable concrete because of its microscopic spherical particle structure, which is even finer than cement. It also possesses a certain level of reactivity. Adding fly ash to cement can partially replace cement and improve the fluidity of the concrete mixture, significantly enhancing its pumpability. Moreover, fly ash contributes to the long-term strength and durability of concrete.
19. Testing Parameters for Fly Ash upon Arrival
The following parameters should be tested for fly ash upon arrival: fineness and water demand ratio, with the water demand ratio being the critical factor. If the fineness is slightly beyond the standard but the water demand ratio meets the requirements for Class II, the fly ash can be used; otherwise, it should not be used.
20. Understanding Concrete Admixtures
Concrete admixtures are additives used to enhance the performance of concrete mixtures.
21. Differences between Water Reducers and Pumping Agents
Water reducers are admixtures used to reduce the water content while maintaining the workability and improving the strength of the concrete mixture. Pumping agents, on the other hand, primarily consist of water reducers with a small amount of plasticizing agents, aiding the pumping process of concrete.
22. Types of Concrete Admixtures
Concrete admixtures include water reducers, pumping agents, retarders, accelerators, early strength agents, antifreeze agents, antifreeze pumping agents, expanders, waterproofing agents, and more.
23. Testing Parameters for Pumping Agents
The following parameters must be tested for pumping agents: water reduction rate, setting time, variation in slump flow, air content, and 28-day compressive strength. These tests help ensure the quality and performance of the pumping agents.
24. Ideal Testing Conditions for Pumping Agents
Good-quality pumping agents should exhibit the following characteristics during mix ratio testing: a water reduction rate of no less than 20%, excellent workability of the concrete mixture, good mortar adhesion to aggregates with easy flow, and slump loss within 50mm after a certain period. Conversely, if some aggregates are not coated with mortar, resulting in poor flowability and a slump loss exceeding 80mm, it indicates poor quality of the pumping agent batch.
25. Recommended Water Sources for Concrete Mixing
The following water sources are recommended for concrete mixing: freshwater, tap water, groundwater, potable water, recycled water, and wash water from the batching plant (partially used). Industrial wastewater, domestic wastewater, and seawater should not be used.
Conclusion
Understanding the key facts and considerations regarding concrete materials based on ready-mix concrete plants is essential for successful construction projects. By carefully selecting the right components and adhering to quality requirements, builders and engineers can optimize the properties and performance of concrete, ultimately leading to durable and efficient structures.
Contact Information
E-mail: market@smachine1983.com
Wechat/WhatsApp: +86 19913897707
Website: http://www.smachine1983.com
Zhengzhou Smart Machinery Manufacture Co., Ltd.