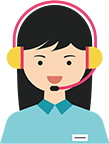
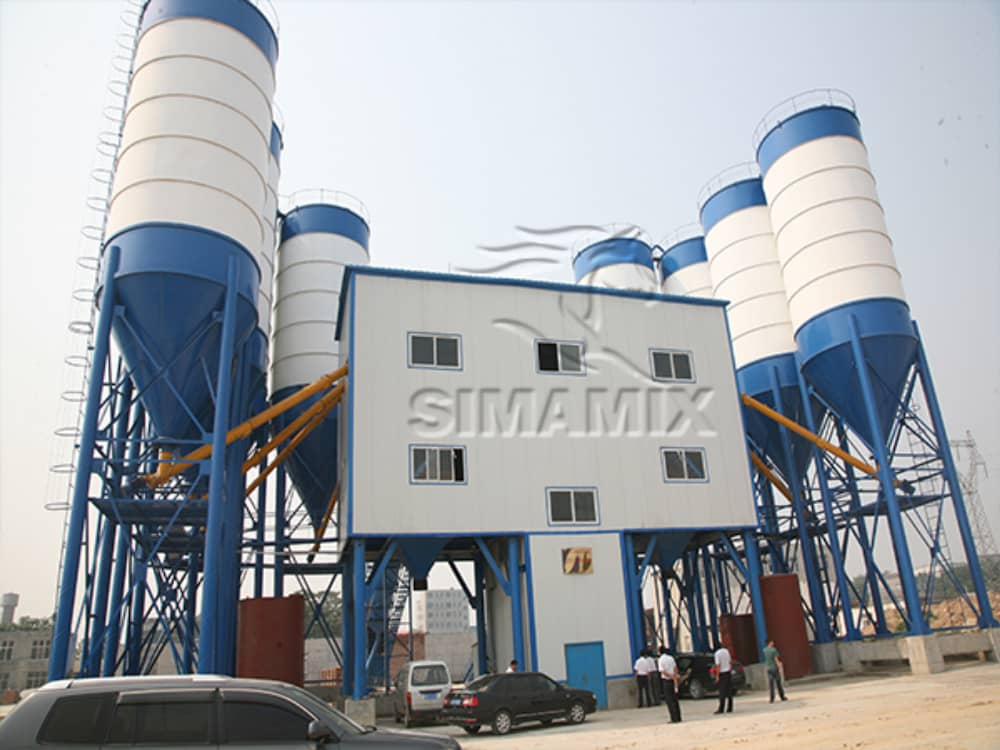
Essential Classification and Maintenance Methods for Concrete Mixers
Concrete mixers play a crucial role in the construction industry by mechanically blending cement, sand, aggregate, and water to create concrete mixtures. Understanding the different types of concrete mixers and implementing proper maintenance techniques is vital to ensure their longevity and optimal performance.
Classifying Concrete Mixers by Drum Shape
Concrete mixers can be classified based on their drum shape, which directly influences their mixing capabilities and efficiency. The following are the three common types:
- Drum-Type Mixer: This type of concrete mixer features a cylindrical drum that rotates on a horizontal axis. It allows for thorough mixing of ingredients, ensuring a consistent mixture.
- Tilting Drum Mixer: A tilting drum mixer has a conical-shaped drum that can be tilted forward or backward to discharge the concrete. This design offers enhanced control over pouring and is particularly useful for smaller projects.
- Pan Mixer: The pan mixer, also known as a circular disc mixer, has a flat, circular-shaped pan where the mixing takes place. It provides efficient mixing by utilizing a combination of gravity and friction.
Categorizing Concrete Mixers by Mixing Principle
Concrete mixers can also be categorized based on their mixing principles, which dictate how the ingredients are blended. Here are two common types:
- Gravity or Fall-Type Mixer: In a gravity or fall-type mixer, the ingredients are allowed to fall into the mixing drum due to their weight. The rotation of the drum facilitates thorough mixing, resulting in a homogeneous mixture.
- Forced or Compulsory Mixer: A forced or compulsory mixer utilizes blades or paddles to forcefully mix the ingredients. This design ensures a more vigorous and consistent blending process, ideal for producing high-quality concrete.
Differentiating Concrete Mixers by Work Nature
Concrete mixers can be further differentiated based on their work nature, which determines their operational characteristics. The following are two main types:
- Batch Mixers: Also known as periodic mixers, batch mixers are designed to handle discrete batches of concrete at a time. They are suitable for projects where specific quantities of concrete are needed, and the mixing process occurs in separate cycles.
- Continuous Mixers: Continuous mixers, as the name suggests, facilitate a continuous and uninterrupted mixing process. They are commonly used for large-scale projects where a continuous supply of concrete is required.
Exploring Concrete Mixers Based on Work Transmission
Concrete mixers can be classified according to their methods of work transmission, which determine the mechanisms involved in the mixing process. The main transmission types include:
- Friction Drive Mixer: Popularly known as friction mixers, these concrete mixers rely on friction to drive the mixing drum. They are often equipped with a clutch system for enhanced control over the mixing speed and direction.
- Gear Drive Mixer: Gear drive mixers, sometimes referred to as ring gear mixers, employ gears to drive the rotation of the mixing drum. This design ensures reliable and efficient mixing performance.
Additionally, concrete mixers can be further categorized into two types based on their drum structure:
- Split-Drum Mixer: Split-drum mixers feature a design where the drum can be divided into two separate parts. This allows for easier maintenance and repair, as well as the ability to mix different concrete types without contamination.
- Trough Mixer: Trough mixers, also known as horizontal-axis mixers, have a drum that is positioned horizontally. This design provides excellent mixing efficiency and is commonly used in large-scale construction projects.
Maintenance Guidelines for Concrete Mixers
Proper maintenance is essential to ensure the longevity and reliable performance of concrete mixers. Here are some crucial maintenance practices:
- Pre-Work Inspection: Before each shift, it is important to run the mixer empty for 1-2 minutes while adding water to the mixing drum. This step helps check the reliability of the clutch and braking system.
- Cleaning and Debris Removal: Regularly clean the mixer's body to remove any dirt or obstructions that may hinder its performance.
- Choosing High-Quality Bearings: When conducting maintenance or repairs, ensure that high-quality bearings are used to maintain the mixer's technical performance and reliability.
- Lubrication and Electrical Check: Regularly inspect and lubricate all lubrication points, check the electrical circuitry, and ensure proper functioning of control equipment as per the manufacturer's recommendations.
- Post-Work Cleaning: At the end of each shift, thoroughly clean the concrete mixer to remove any residual concrete, ensuring a clean and efficient operation in subsequent uses.
- Monitoring Operational Performance: During the operation of the concrete mixer, regularly monitor the motor, gearbox, and gear noise levels to ensure they are within acceptable limits. Also, pay attention to the temperature rise, as excessive heat can indicate potential issues.
By following these maintenance guidelines, concrete mixer owners can significantly extend the lifespan of their equipment and ensure consistent performance for their construction projects.
Contact Information
E-mail: market@smachine1983.com
Wechat/WhatsApp: +86 19913897707
Website: http://www.smachine1983.com
Zhengzhou Smart Machinery Manufacture Co., Ltd.